4-rail tamping
This mode uses four tamping unit segments. The outer segments can be slewed out far enough that the long bearers of the diverging rail in the turnout can also be tamped. This is an ideal supplement to automated synchronous 3-rail lifting. Positioned on transverse guide columns, the inner tamping units can be displaced laterally. This enables them to be operated in the area inside and outside the respective rails. All four tamping units can be turned and thus adapted to the slanting position of the sleepers.
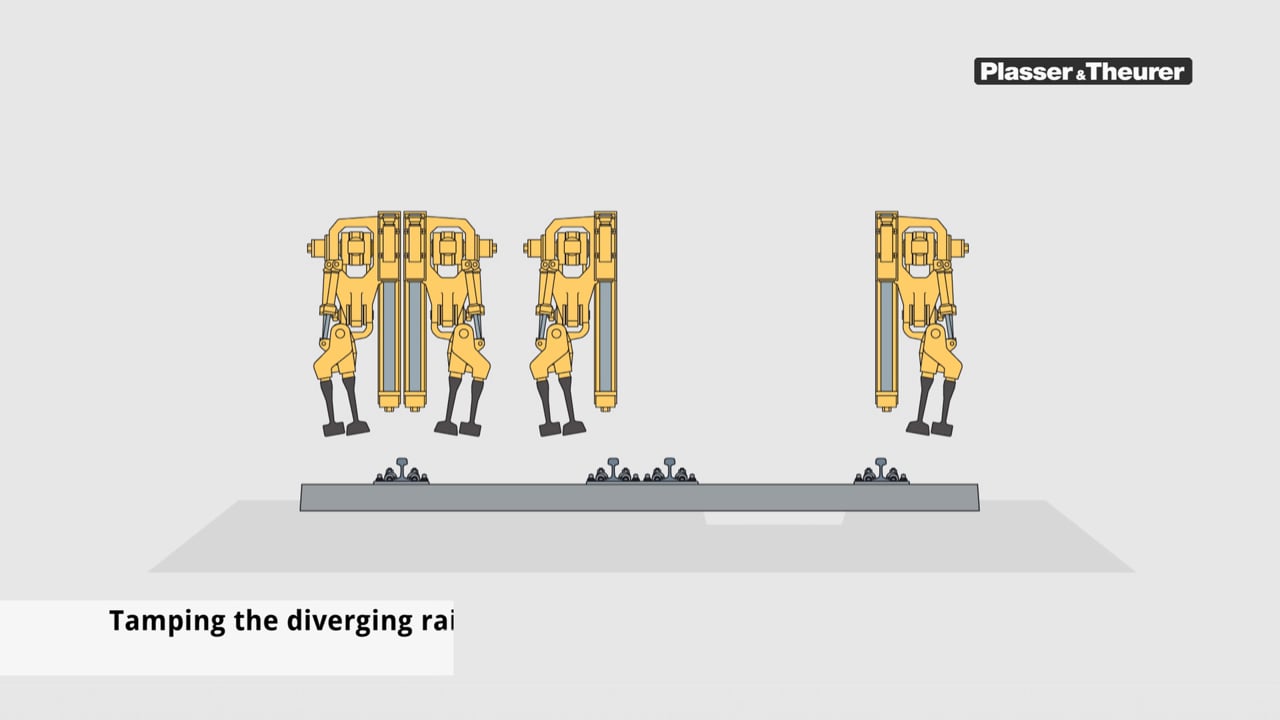