Rotation speed modulation of tamping units
In addition to noise reduction, the rotation speed modulation enables fuel savings of up to 10 %. Moreover, it significantly reduces wear on the tamping units.
0 %
fuel savings
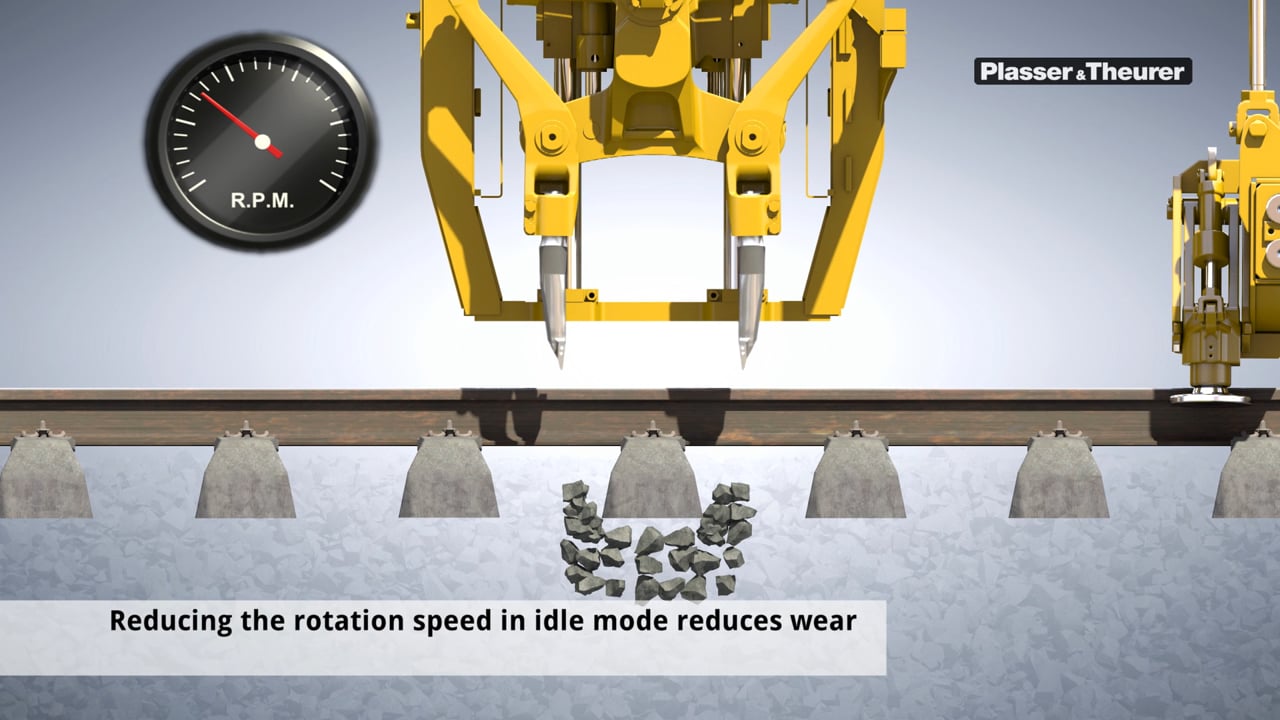
In addition to noise reduction, the rotation speed modulation enables fuel savings of up to 10 %. Moreover, it significantly reduces wear on the tamping units.
During track tamping, the combined levelling and alignment laser guides the tamping machine according to the precision method. Using this method, the laser beam is displayed on the laser receiver camera (at the tamping machine) and analysed according to its position.
The combined levelling and alignment laser also allows producing a particularly accurate turnout geometry. In doing so, the ideal geometric position of the turnout (in the through rail) is recorded along the laser reference line.
You can choose from a complete range of tamping units for all track and turnout maintenance applications, classified according to output and performance requirements. They are available in various designs and sizes: the perfect fit for all our tamping machines.
The latest track maintenance machines use both the electrical energy from the contact wire and batteries to power the working drive. Our new E³ drive technologies reduce local emissions - of both pollutants and noise – to a minimum on the work site.
At Plasser & Theurer, we have taken the classical tamping machine to a new level. The Unimat 09-4x4/4S E³ uses the electrical energy from the overhead contact line not only for electrical traction during transfer travel. It is also used to power the tamping unit electrically for the first time. The crucial working parameters remain unchanged. If there is no overhead contact line available for current collection, we use a diesel-electric generator to supply electrical power.
30 years ago, a technical concept evolved from an idea to increase the cost efficiency of tamping work. It has continued to set standards even to this day. The technical basis was laid early on: the U-shaped design of the machine's main frame and the positioning of the work units between the axles. However, it was always necessary to accelerate and brake the entire machine mass to be able to tamp. Due to the separation into a continuously moving main frame and a cyclic-action subframe, less than 20 % of the machine mass has to be accelerated and braked.
The standard in user-friendliness and process reliability: the track-geometry guiding computer provides ultimate operating comfort. Equipped with the SmartALC, tamping machines can work according to the precision method or the compensation method. Operators can select one of four pre-defined user profiles provided by the SmartALC to ensure their needs are met perfectly. Using AutoSync, for example, the machine automatically detects track defects.